Scope
This reference manual covers the operation of an OmniTest-5.0 force test stand, intended for use with Mecmesin enhanced load sensors, extensometer devices and other Mecmesin accessories. Operation of additional accessories is covered in separate documentation.
The following manuals may aid you in the use of your test stand:
- Guide to Safe Use of Mains Powered Test stands (part no. 431-398),
- VectorPro™ MT for OmniTest and dVu Test Stands (part no. 431-955),
- Long Travel Extensometer Installation Guide (part no. 431-957),
Important
It is essential that you familiarise yourself with the contents of this Manual and the separate Guide to Safe Use of Mains Powered Test stands (part no. 431-398) before attempting to operate your OmniTest-5.0 Test stand.
[toc]
Items Supplied with your Test Stand
When ordering your OmniTest-5.0 test stand you will be supplied with the following parts:
- OmniTest-5.0 test stand,
- Mains cable,
- Document: A Guide to Safe Use of Mecmesin Mains Powered Test stands,
Note: Accompanying VectorPro™ MT software may be supplied either via a physical flash drive or software download link
Accessories
For a full range of enhanced load sensors (ELS), extensometers and accessories, please go to the Mecmesin website www.mecmesin.com, or your local distributor, as listed on the back cover of this document.
- For connection of the stand to your computer system a Mecmesin supplied 2m USB B to USB A cable communications cable is required (part no. 351-093).
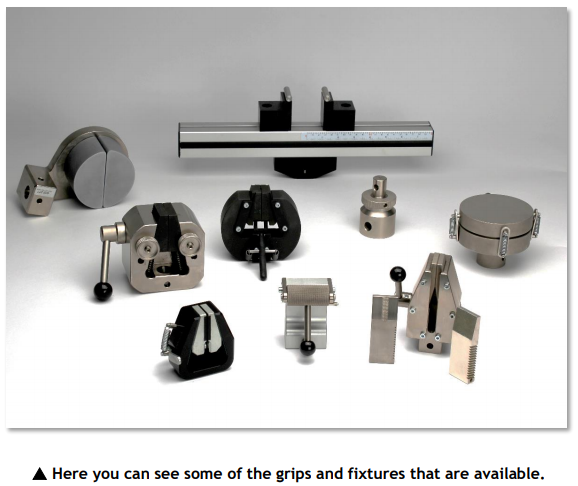
OmniTest 5.0 System Diagram
- Easily accessible upper and lower safety limit switches
- ELS S-beam variant
- Front control panel
- Multi-function scroll
- Emergency stop wheel
- Mecmesin LTE-700, long travel extensometer (Optional accessory, part no. 432-700)
- Mecmesin 5kN eccentric roller grips (Optional accessory, part no. Mec7-5)
- T-slot profile runs down either side of the main column, allowing for mounting of accessories such as tablet PC’s
Initial Setup
Unpacking the Stand
When you first receive the stand please check that there is no obvious damage to the packaging. If there is any sign that the packaging or the test stand itself has been damaged, please contact Mecmesin or your authorised distributor immediately. Do not use the stand until you have done so.
We strongly recommend that the packaging is retained, as this can be useful if the machine needs to be returned for calibration or shipped between sites. Section 1 lists items that should be included with your test stand. Please contact Mecmesin or your authorised distributor if any items are missing or damaged.
Lifting the Test Stand
The unpackaged weight of the test stand is given in the specification table at the back of this manual. Do not try to lift heavy loads unaided. It is advised to use suitable lifting equipment when moving your OmniTest-5.0 system.
Environment Conditions
In line with BS EN 61010-1 it is recommended that your Mecmesin OmniTest-5.0 test stand is operated in an environment that matches the following conditions:
- Indoor use only, recommended to be operated in a lab environment.
- Altitude up to 2 000 m;
- Temperature range between 10 °C to 40 °C. Please note that the instrument should not be used for long durations at higher temperatures.
- The maximum relative humidity is 80 % for temperatures up to 31 °C decreasing linearly to 50 % at 40 °C. It is crucial that the surrounding environment does not cause water to form on the device.
- Mains supply voltage fluctuations up to a maximum of ±10 % of the nominal voltage.
- The environments should also take considerations of excessive dust or metal particulates as ingress of these into the device can cause damage to the system.
Mains Power Supply
OmniTest-5.0 test stands can be used on 110–120 or 220–240 V ac 50-60 Hz supplies. The rear fuse carrier will be set for your local requirement but is reversible, so should you replace a fuse, the correct local voltage must be selected.
The voltage that is selected is indicated by which arrow is pointing to the white line located at the bottom of the device. This is illustrated in the image below, shown within the red circle
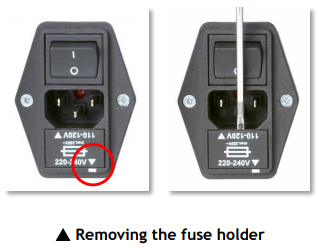
ELS: Enhanced Load Sensor
Enhanced load sensors or ELS for short, are smart devices used to capture load readings for OmniTest-5.0 test stands, all calibration information is held on the individual load cell meaning they can be swapped from system to system and the calibration will follow with no input required.
These load cells are available in a range of sizes and designs to best suit your requirements.
See the specifications section of this document for details relating to capture rate and accuracy.
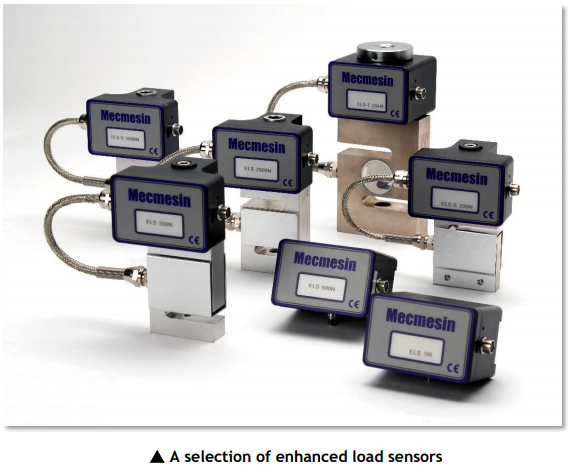
Fitting an ELS to your Test stand
The OmniTest-5.0 has a dovetail bracket attached to the moving crosshead, which tightens by using an Allen key on the embedded screw.
To fit your ELS to your test stand slide the load cell sideways onto the dovetail and tighten the grub screw (circled below in red) located in the dovetail using a suitable Allen key.
To prevent damage, do not over-tighten the grub screw in the dovetail when a gauge bracket is not present.
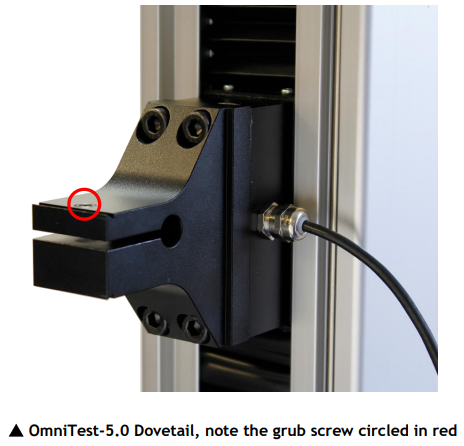
Note: Take care when handling low capacity ELSs such as a 5N cell, as damage can easily occur from mishandling.
It is also important to ensure that attached grips and fixtures do not overload the ELS. If in doubt please check the weight of any addition grips and fixtures prior to fitting these.
Connecting an ELS to the OmniTest-5.0
To connect your ELS to your OmniTest stand simply plug the 6-pin connector located on the machines crosshead into the ELS fitted.
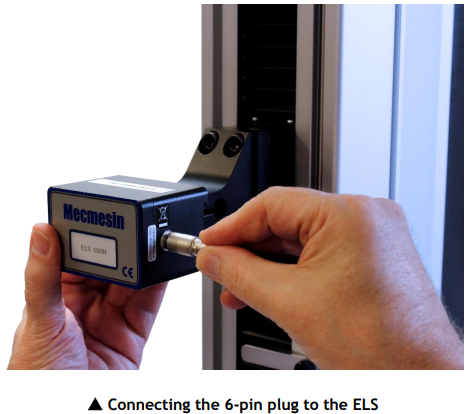
As enhanced load sensors are ‘smart’ devices all calibration and capacity information is passed to the stand automatically as the sensor is connected.
Connecting the OmniTest-5.0 to a PC
To connect your OmniTest-5.0 test stand to VectorPro™ MT software, connect the USB B port to a PC using cable part no. 351-093.
Important! Please install VectorPro™ MT software on your desired PC before connecting the test stand to your PC.
Cable Management
It is essential that no cables are permitted to interfere with the controls or any moving parts.
Attaching Grips and Fixtures
For flexible attachment of a variety of accessories and improved alignment, the OmniTest-5.0 is fitted with an anvil plate to accept fixtures with different screw threads.
This is attached with four bolts using an Allen key. For alignment, the anvil plate can be loosened, moved forwards or back, and the bolts retightened.
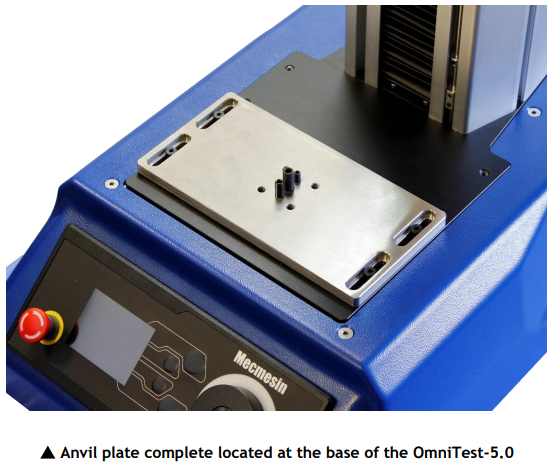
Upper grips and accessories are attached directly to the ELS device being used.
QC adapters are available and can be fitted directly to the anvil plate or through a Mecmesin LTE-700 extensometer.
Setting the Limit Stops
Limit stops help prevent damage to load cells and fixtures by stopping the crosshead movement before the moving fixtures come into contact with static parts of the stand. Their positions are adjusted after the fitting of fixtures and test samples.
There are two manually-set limit stops, located for your convenience, on the front of the OmniTest-5.0. These are set by loosening the thumb-screw, moving the stop to a new position and retightening. When the crosshead meets a stop, it activates a switch. This will stop crosshead movement at an upper or lower limit.
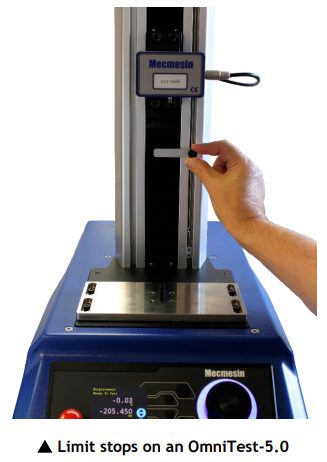
Test Stand States
The test stand can be in one of five states:
- Test readiness - ready to start, or complete,
- Testing – test operation sequence is running,
- Stopped - test interrupted or emergency stop pressed,
- Jog mode - for jogging or positioning the crosshead manually,
- Settings menu – for adjusting your test stands settings
In each state, the selector buttons have functions described by the on-screen icons.
Front Panel Controls
Emergency Stop Button
Push to immediately stop crosshead movement. Rotate the button to release it and resume crosshead control. If pressed during a test, do not simply restart a test, ensure you remove any residual force using the test stand’s jog controls.
Multi-function Scroll Wheel Control
Scroll Wheel Colours
The LED light ring surrounding the scroll wheel shows three colours, indicating three states, these states are:
Jog Mode
When in jog mode the wheel drives the crosshead directly up (clockwise) or down (anticlockwise). This offers more variable control when compared to the two fixed speed jog control buttons (circled in red below).
The scroll wheel can also be used as a speed controller. The jog buttons move the crosshead at the set speeds (configured in the ‘Jog Settings’ menu picture below), but rotating the wheel clockwise whilst holding a jog button will increase the speed and rotating the wheel anticlockwise whilst holding a jog button will decrease the speed.
OmniTest-5.0 test stands also feature a precision jog mode, rotating the scroll wheel while holding the central scroll wheel button moves the test stand at its minimum speed, this is useful when fitting specimens into grips for example.
Navigational Control
The scroll wheel can also be used to navigate the menus. When in a selection menu, the scroll wheel cycles through the selections and their values. This is an alternate navigational option to using the up and down arrow buttons.
The Button
The central button is used to confirm a menu selection. It is equivalent to the tick button. It can also be used to activate fine jog control, by rotating the scroll wheel while holding the central scroll wheel button moves the test stand at its minimum speed.
OmniTest Display Panel
The display indicates the stand status, displays live values and is used to configure the test stands settings.
The purpose of the four multi-function button is indicated on screen by an adjacent icon. Below is an image showing a typical example of the on-screen icons in relation the physical buttons.
On-Screen Icons
On-screen icons vary depending on the current state of the test stand and what functions the physical buttons perform at that point. Below is are reference tables to help explain the icon definitions.
A: Pre-Test
Icon Action No ELS connected. Go to jog mode. Go to settings. Move to the home position (zero position from the beginning of the previous test). Top button is ‘confirm’ Upper middle button is ‘up’ Lower middle button is ‘down’ Lower button is ‘back’
B: Test Stop
Icon Action Stop test: This stops crosshead movement, leaving the stand in a state of test readiness. The message is ‘Interrupted: User’ and the test readiness buttons (A) are displayed as well as the home button. Emergency stop button pushed: Message: ‘Emergency Stop!!!’. Release the emergency stop to regain control and remedy the situation before resuming testing. Note there is no on-screen icon for the emergency stop. Upper limit switch triggered: The crosshead has reached the upper travel limit, as set by the OmniTest-5.0’s limit switches, and stopped. Further travel in this direction is prevented. Lower limit switch triggered: The crosshead has reached the lower travel limit, as set by the OmniTest-5.0’s limit switches, and stopped. Further travel in this direction is prevented.
C: Jog Mode
Icon Action Zero (tare) all system values. Move the crosshead upward at the set jog speed. Crosshead has reached an upper limit (load signal from a connected gauge, set to Stop, or a limit switch) and stopped. Move the crosshead downward at the set jog speed. Crosshead has reached a lower limit (load signal from a connected gauge, set to Stop, or a limit switch) and stopped.
D: Settings Menu
Icon Action Confirm selection (or press the scroll wheel button). Navigate up a menu selection or value (or turn the wheel clockwise). Navigate down a menu selection or value (or turn the wheel anticlockwise). Go back to the previous screen.
OmniTest™ 5.0 Settings
All settings are made by moving the selection marker to the required item or digit and confirming with the tick button or using the central scroll wheel button.
Settings: Jog settings
Within the jog settings menu, you can configure the jog speed and force limits while in jog mode. Below is a detailed breakdown of each setting and the options available for each setting. Setting Action Range Up Speed Configure the jog speed in an upward motion 0.050 to 1200 mm/min 0.002 to 47.24 Inch/min Down Speed Configure the jog speed in a downward motion 0.050 to 1200 mm/min 0.002 to 47.24 Inch/min Tension Limit Configure the tensile force limit for jog operations Up to 2500N Up to 562 lbf Compression Limit Configure the compressive force limit for jog operations Up to 2500N Up to 562 lbf
Settings: PIN Code
Within the PIN code menu, it is possible to set a four-digit number that can be used to lock the menu feature of your OmniTest-5.0. Please note once this has been set you cannot access the menu without the PIN, so it is crucial that you keep a record of this safe. To remove the PIN code set the four digit number to ‘0000’.
Settings: Pre-load Threshold
This menu displays the pre-load threshold as configured by VectorPro™ MT, changes here will be overwritten by VectorPro next time you start a test.
Settings: Information
This screen is used to display key information relating to your OmniTest-5.0 and connected ELS. Here you can see software, hardware and firmware properties as well as the calibration date for the test stand and the number of overloads that have occurred for the current ELS.
Rear Connectors Panel
OmniTest™ 5.0 Specification
OmniTest - 5kN
Rated capacity kNKn5
kgf500
lbf1100
Number of ballscrews 1
System accuracy Class 0.5, according to the requirements of the BS EN ISO7500 (requires optional on-site UKAS accredited system calibration)
Maximum sampling rate 500Hz
* Measured without fixtures ** Measured on centreline of load sensor Connectivity USB port, extensometer input, 3 x low voltage additional sensor inputs with future expansion capability PC requirements (recommended) Intel Core i5 processor, 8GB RAM, one USB 2.0 or 3.0 port, SSD hard drive with 10GB free space, screen resolution 1920x1080 full HD PC requirements (minimum) Intel/AMD dual core processor with 2 GHz or faster clock speed, 4 GB RAM, one USB 2.0 or 3.0 port, hard drive with 10 GB free space, screen resolution 1080x720 Compatible OS: Windows 7 or Windows 10 (32 or 64 bit) Recommended OS: Windows 10 Pro 64 bit Data output You can export as PDF, XLSX, CSV, TXT, Email and image files Software and communications Operating system (OS) Kn 5 kgf 500 lbf 1100 Environment specification Operating temperature Accuracy Accuracy Maximum power requirement Enhanced Load Sensors (ELS) Sensor measurement accuracy Sensor measurement resolution Internal sampling rate Voltage Speed Speed range Speed resolution Dimensions Height System accuracy Resolution OmniTest-5kN Rated capacity kN Number of ballscrews Displacement Crosshead travel*