Accurate and Repeatable Painless syringe testing
Introducing the syringe
The medical syringe itself is actually just the cylinder and plunger mechanism by which liquid medication is delivered to the patient, but by connecting it to other upstream or downstream components, a valuable and versatile system is created. The final connection is often, of course, a needle—creating a needle injection system (NIS)—but not in every case; an oral syringe is used to ‘point and squirt’ directly from the barrel tip into the mouth. The differing designs of these sub-components and connectors mean that often quite complex interactions occur as the syringe is assembled, prepared, used, potentially re-used, and stored. During its lifecycle, the device not only comes into contact with the patient and the administering healthcare professional—sometimes the patient themselves—but also its original packaging, medicine vials and finally, disposal containers.
Testing times
The medical devices and pharmaceuticals sector is highly regulated, driven by compliance and auditing processes. Syringe manufacturers must ensure thorough testing has been performed which is appropriate to the syringe’s specific design. International standards bodies publish procedures enabling manufacturers to test the functionality and integrity of each subcomponent and sub-assembly that may be part of a complete syringe system. These international test standards are important not only in manufacturing quality control but also form the basis of functional performance and new product development optimisation in design and R&D departments. In order to confidently meet standards, a syringe manufacturer must be able to measure the relevant parameters required to push, pull and twist the various mechanisms which may all apply to a single, complete system. They must also ensure that the results are accurate, repeatable and reproducible—and formally documented.
Resolution not revolution
In terms of functionality, quite light loads are often applicable—devices must operate easily, assemble reliably and be able to be used by the elderly and infirm. In contrast, the product must be strong enough to perform as expected and resist forced or accidental disassembly. Accuracy of instrumentation reading is vital therefore in testing to these finely balanced requirements. By switching to a loadcell of a capacity close to the expected maximum load, the accuracy of the reading is optimised for the specific test being performed. Also vital, is appropriate resolution of the reading where a value indicating a ‘pass’ or ‘fail’ is needed. Again, the ability to fit a correctly matched loadcell provides this ability to differentiate between the two conditions.
Measuring with optimal accuracy is all well and good as long as the correct condition is being measured. Holding the test specimen in the desired orientation and applying the representative loading precisely is achieved by the use of suitable fixtures. The grips must hold the specimen securely to avoid slippage, yet not deform it or introduce unrepresentative loads. Mecmesin’s standard interchangeable accessories enable an extensive range of medical device tests to be performed ‘off the shelf’. However, for particularly innovative or intricate designs, Mecmesin provides a service to custom-design and manufacture bespoke fixtures exactly to the customer’s specification.
Although cost-effective, simple-to-use, manually operated force and torques testers are available—for medical and pharma industry use it is essential to have a motor-driven machine, incorporating software control. Some test standards also explicitly stipulate the use of a motor-driven tester. The motor delivers constant speeds of extension/compression or rotation, and the software enables a degree of automation, performing the procedural steps and calculating important values from the measured data. Furthermore, this sector requires software to provide traceable results, storage of raw data, a robust audit trail and full operator security.
Examination of the problem
Syringe plunger and barrel
The smooth and consistent operation of the plunger is essential when administering drugs from the syringe, whether manually or via an automated pump device. High forces or erratic movement can result in unnecessary patient discomfort. Tests on the plunger-cylinder mechanism focus not only on the design’s inherent functional performance and leakage prevention, but also support quantification of injectability and ‘syringeability’.
A Universal Testing Machine is used to move the syringe plunger at a controlled speed to aspirate and expel water, whilst the force exerted and the plunger travel are recorded. This mechanical testing enables the frictional and lubricity parameters of the plunger sealing head and barrel to be determined:
- The initial 'break-loose’ force to start the plunger moving from its resting position.
- The sustaining 'glide’ force to keep the plunger moving.
- The minimum, maximum and mean forces experienced during the return stroke of the plunger.
These are the key events that the instrument’s software must recognise in order to fully characterise the syringe’s performance. To meet a global manufacturer’s need to increase production during the worldwide COVID vaccination programme, Mecmesin added a 12 specimen capacity to the syringe tester and provided software automation to run the test on the complete batch without operator intervention.
Needles
Hypodermic needles are tested to determine how their design influences the ease of insertion and retraction from the skin—a key factor influencing patient comfort and skin trauma. Designs of needles may differ according to the intended injection routes. Similarly, needles are tested to determine how well they pierce the elastomeric membrane of a vial closure without producing unintended rubber fragments. The characterisation of needle performance – namely for point sharpness, the effectiveness of the bevelled tip geometry and the frictional forces experienced along the shaft—is easily established by a computer-controlled compression test system. The real-time graphical force profile may be analysed for key areas of interest during the penetration (and extraction) stages, including:
- The initial peak force at which the needle tip first pierces the test ‘skin’ specimen, Point (A)
- The intermediate cutting force as the bevelled cutting edges continue through the hole, expanding it wider, Junction (B)
- The overall peak cutting force as the hole is fully opened, Heel (C)
- The frictional ‘drag penetration force’ experienced as the needle shaft slides through the hole to the required depth – an indication of needle-shaft lubricity.
- The tensile extraction force as the needle is withdrawn, may be measured to further differentiate designs and lubricity. To simulate real-life use of needles, a custom fixture allows adjustment of the angle of insertion into the substrate.
Hub-to-syringe connection
There are 3 main types of NIS syringe construction. Two of the most implemented are the Luer Lock syringe for detachable needles—which attach by a twist-fit thread to form the seal—and the Luer Slip syringe for detachable needles—which attach by a push fit with a small twist on a 6% conical taper. These designs need mechanical testing of the joint between hub and syringe to ensure a leak-free connection and optimal performance under normal use. A complete suite of tests would comprise:
- Ease of assembly of the connector.
- Axial resistance-to-separation force of the connector.
- Connector resistance to separation by unscrewing; torque.
- Resistance to overriding of the connector; torque.
- Disconnection; unscrewing release torque.
Some international standards describe test methods that involve simultaneously applying a defined axial load and torque to the Luer connection, then observing whether it has separated. This requires a unique testing system that can both apply force and measure torque—especially at the low values resulting from small-bore connectors—making the Mecmesin Helixa ideal for testing of this nature.
The final diagnosis
In such a compliance-driven sector as medical and pharma, quality assurance to meet legislative standards in both design and manufacturing functions is a critical condition. With constantly evolving external factors such as the move to more sustainable new materials, cost reduction targets, and product innovation also changing the landscape, ensuring consistent functional performance is a challenge. For confident medical device testing to be as painless as possible, the implementation of a versatile test system with carefully selected accessories is prescribed.
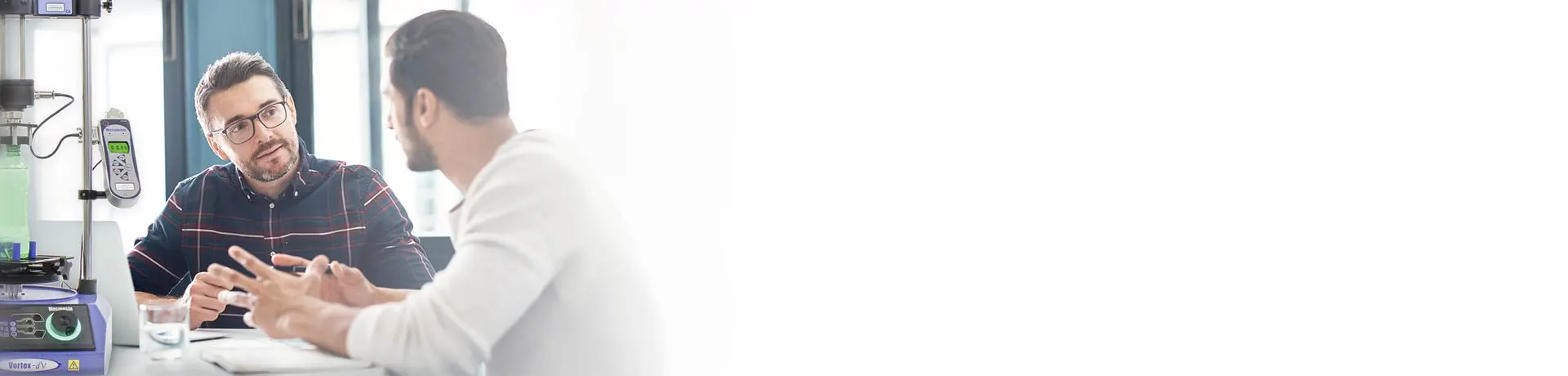